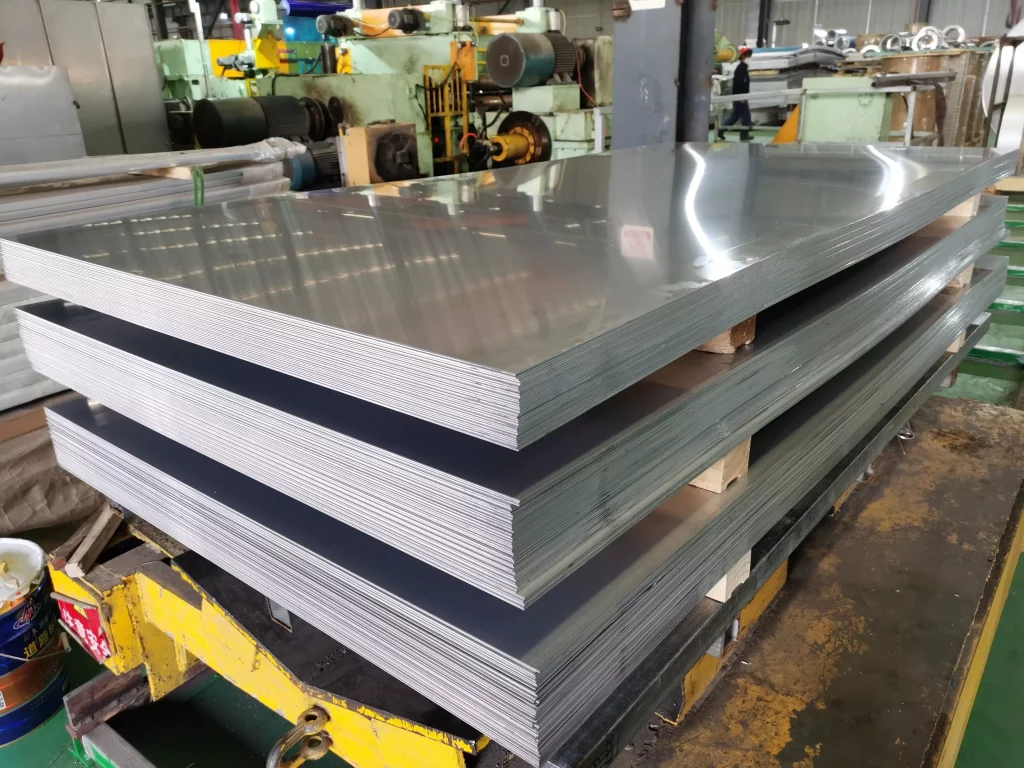
5754 Aluminum Plate
- Product: Aluminum Sheet/Plate
- Alloy: 1050, 1060, 1100, 1070, 3003, 3004, 3105, 5052, 5754, 5083, 6061, 6063, 6062, 7075, 8011
- Temper: H12, H14, H16, H24, H26, H32, O, H112, T3, T6, T4, T651, etc.
- Surface: Mill finish, color coated, embossed, engraving, checkered
- Thickness: 0.2-200mm
- Width:10-2600mm
Description
5754 aluminum plate is a medium-strength alloy known for its excellent corrosion resistance, weldability and formability. As a typical Al-Mg series alloy, 5754 is widely used in automotive manufacturing, such as doors, molds and seals, and the can industry due to its excellent processing performance and corrosion resistance. Our plates are available in a variety of sizes and thicknesses, ensuring they meet the strict quality standards required for your project. Choose our 5754 aluminum plate, a material that combines durability and ease of use, backed by our factory expertise and global supply capabilities.
| 5754 Aluminum Plate Parameters
Product | 5754 Aluminum Plate |
Temper | H12, H14, H16, H24, H26, H32, O, H112, T3, T6, T4, T651, ect. |
Surface | Mill finish, color coated, embossed, engraving, checkered |
Thickness | 0.2-200mm |
Width | 10-2600mm |
Length | 100-100000mm |
Packing | Wooden pallet |
Payment | T/T, L/C 100% at sight |
MOQ | Normally 5 tons, special require need discuss |
Delivery time | 1-3 days for spot goods, 10-15 days for normal size, 15-25 days for special size |
| Chemical Composition of 5754 Aluminum Plate
Element | Ai | Mg | Mn | Cr | Si | Fe | Cu | Zn | Other | |
5754 | Each | Total | ||||||||
remainder | 2.6 – 3.6% | 0.4 – 0.8% | 0.05 – 0.25% | 0.40% | 0.40% | 0.10% | 0.25% | 0.05% | 0.15% |
| Advantages of 5754 Aluminum Plate
- Marine-Grade Corrosion Resistance: The high magnesium content provides superior resistance to corrosion, especially in marine applications, where exposure to saltwater and humid air would typically degrade other materials.
- High Strength: The alloy’s strength makes it suitable for heavy-duty applications, such as in the manufacturing of ship hulls, offshore structures, and other components that require robust structural support.
- Weldability: The material’s excellent weldability allows for the creation of strong, stable, and durable welded joints, which is crucial for many construction and fabrication processes.
- Formability: Despite its strength, 5754 aluminum plate is formable, enabling the production of complex shapes and components that can meet the design requirements of various projects.
- Cost-Effectiveness: It offers a balance of performance and cost, providing a high level of corrosion resistance and strength without a prohibitive price tag.
- Recyclability: As with all aluminum alloys, 5754 is recyclable, making it an environmentally friendly choice that aligns with sustainability goals.
- Aesthetic Appeal: The mill finish provides a clean, uniform appearance that is suitable for both functional and aesthetic applications.
| Why Choose Us
- Innovative Custom Formulations: We don’t just offer standard aluminum products; we specialize in developing custom aluminum alloys tailored to specific industry needs, providing a solution that no other supplier can match.
- Sustainability Leadership: Our production processes are designed with sustainability in mind, from energy-efficient manufacturing to the use of recycled materials, positioning us as an industry leader in eco-friendly aluminum products.
- Exclusive Technology: We utilize proprietary technology that enhances the properties of our aluminum products, such as increased strength-to-weight ratios or unique surface treatments that offer superior resistance to environmental factors.
- Expert Consultation: Our team of experts provides unparalleled consultation services, working closely with customers to understand their unique challenges and offering tailored solutions that are unmatched in the market.
- Integrated Supply Chain Solutions: We offer a seamless, integrated supply chain solution that includes everything from raw material sourcing to finished product delivery, ensuring a level of convenience and efficiency that is unique in the industry.
- Advanced R&D Capabilities: With a state-of-the-art research and development facility, we are at the forefront of aluminum technology, constantly pushing the boundaries of what’s possible with our materials.
- Patented Processes: We have patented processes that give our aluminum products a distinct edge in terms of quality, performance, and applications, which cannot be replicated by competitors.
- Strategic Global Partnerships: Our strategic partnerships with key industry players provide customers with access to a network of resources and expertise that is unique to our company.
- Guaranteed Performance: We offer a performance guarantee on our aluminum products, ensuring customers that our materials will meet or exceed their expectations in real-world applications.
- Cultural Alignment and Ethical Practices: Our company operates with a strong ethical code and a culture that aligns with our customers’ values, building trust and a partnership that goes beyond mere transactions.
- Post-Sale Support and Education: We provide ongoing support and educational resources to help customers maximize the performance of our aluminum products, ensuring they get the most value from their investment.
- Exclusive Access to Niche Markets: We have established channels into niche markets that other suppliers cannot access, offering our customers unique opportunities for growth and expansion.
| process flow diagram
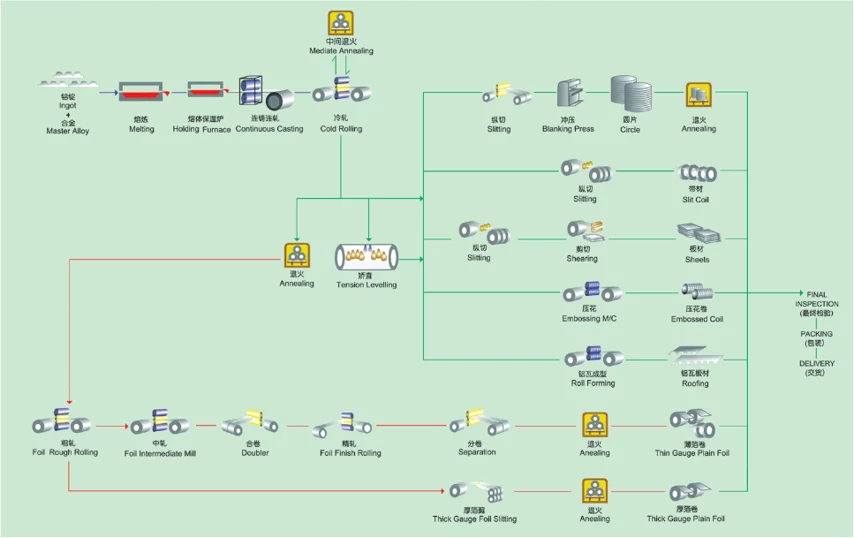
| 8011 Mill Finish Aluminum Plate Production Flow Chart
Hot-rolling
Smelting–standing–casting–fire–hot-rolling–cold-rolling –finished product annealing-packing
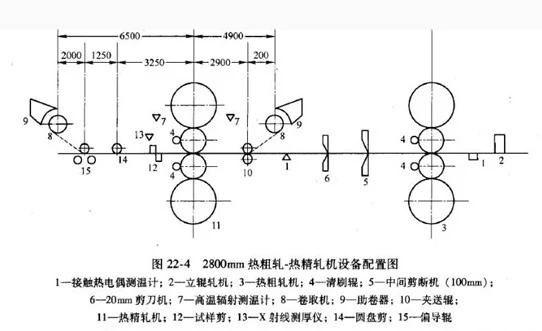
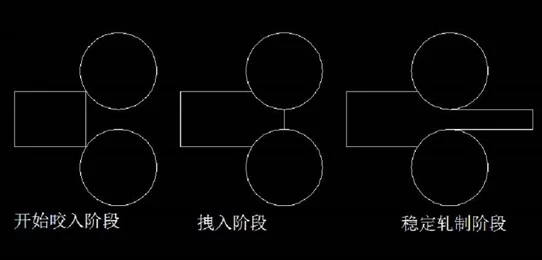
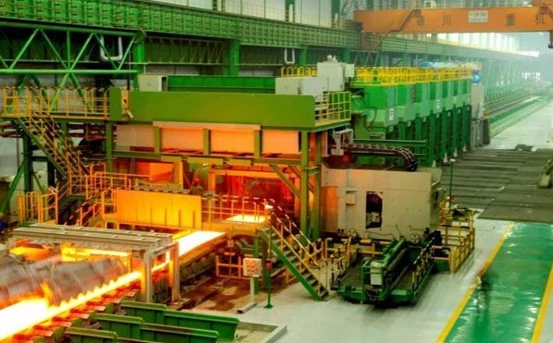
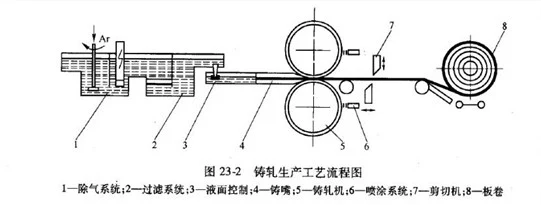
Cast-rolling
Smelting– standing — cast-rolling– cold-rolling– finished product annealing– packing
Casting
The purpose is to manufacture casting components that meet the requirements for a high purity alloy melt and create favorable conditions for casting various shapes.
Several key parameters in the casting process include:
- During the casting process, workers need to continuously add Al-Ti-B wire to refine the grain.
- The temperature generally needs to be set at 1050°C when smelting, with the material’s temperature under constant monitoring, and the metal temperature should be controlled to be less than 770°C.
- At around 735°C, workers need to perform slag operations; this temperature is favorable for the separation of slag from the liquid.
- Generally, two refining processes are required: one using a solid refining agent and the other using a gas refining method.
- After approximately 30 minutes to 1 hour of inert gas purging, workers need to cast in a timely manner; otherwise, re-refining may be necessary.
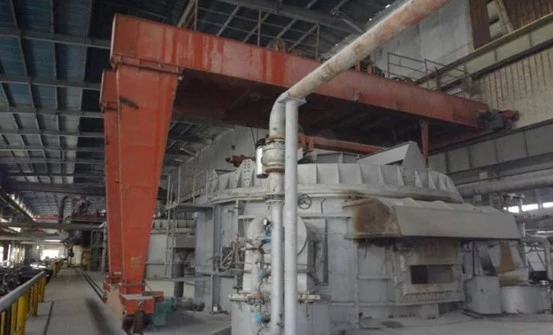
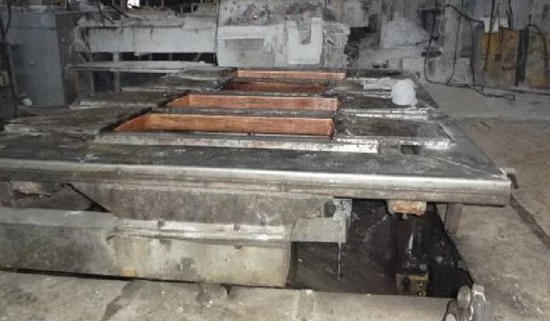
Tension Lever
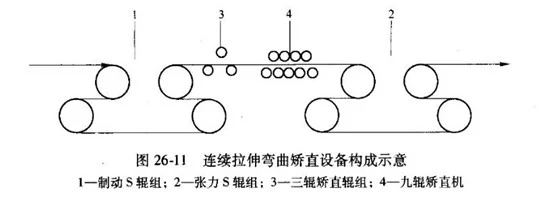
Slitting Mill
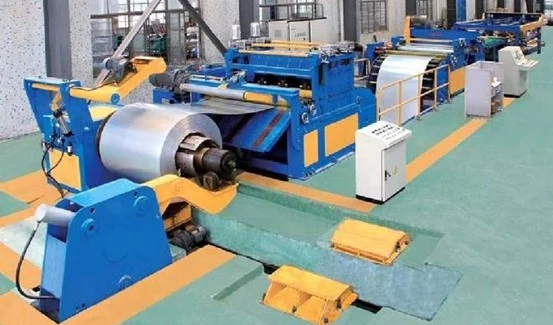
Cross Cutting Mill
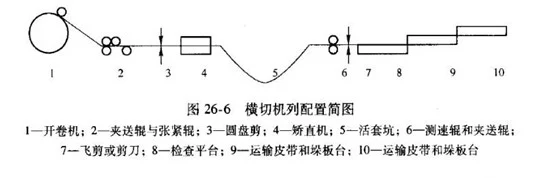
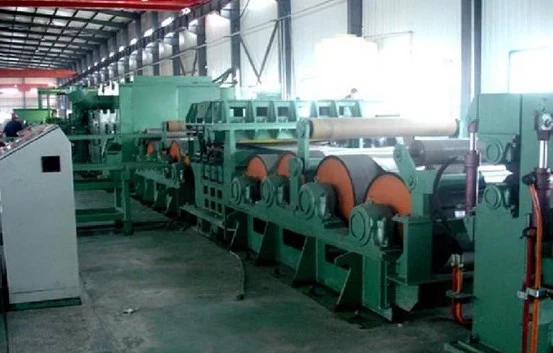
Packing
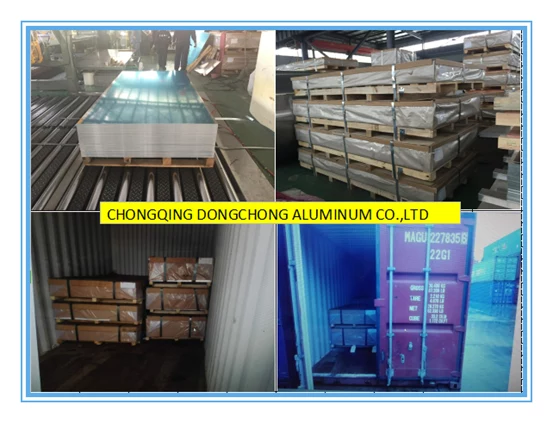
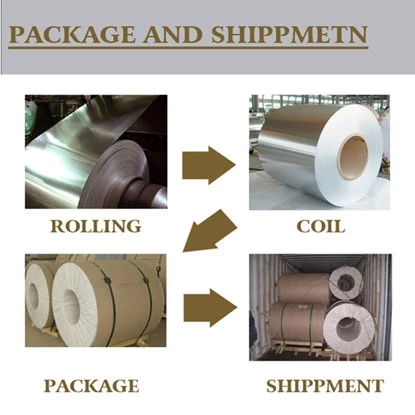